The Crucible of Innovation: How Roman Coin Casting Forged an Artisanal Renaissance
There's a peculiar kind of reverence I feel when holding a worn, ancient object. It's not just the age, the inherent fragility, but the whispered stories embedded within it. When I first began researching Roman coin replicas, it wasn't simply about recreating a piece of currency; it was about touching history, feeling the pulse of an empire. I imagine the hands that originally held these coins – merchants haggling in the Forum, legionaries receiving their pay, citizens participating in the lifeblood of Rome. And surprisingly, the methods used to *make* those coins, and subsequently to recreate them today, reveal a fascinating story of technical innovation and a surprisingly robust artisanal ecosystem.
We often picture the Roman Empire as monolithic, a grand design dictated by emperors and senators. And while imperial decree certainly played a role in coinage – the imagery, the inscriptions – the sheer scale of coin production necessitated a decentralized network of mints and workshops. These weren't just state-run factories; they were hubs of skilled labor, where metalworkers pushed the boundaries of casting and striking techniques. And understanding how we recreate these coins today reveals an echo of that same ingenuity.
From Rudimentary Molds to Refined Techniques
Early Roman coinage, particularly during the Republic, often relied on the 'lost-wax' casting process, a technique dating back millennia. Think of it like creating a sculpture from metal. A wax model of the coin's design is carefully crafted, then encased in clay. The wax is melted out (hence ‘lost-wax’), leaving a cavity which is then filled with molten metal – typically bronze or silver. Once cooled and hardened, the clay mold is broken away, revealing the finished coin. The quality, naturally, depended heavily on the skill of the craftsman and the care taken at each stage.
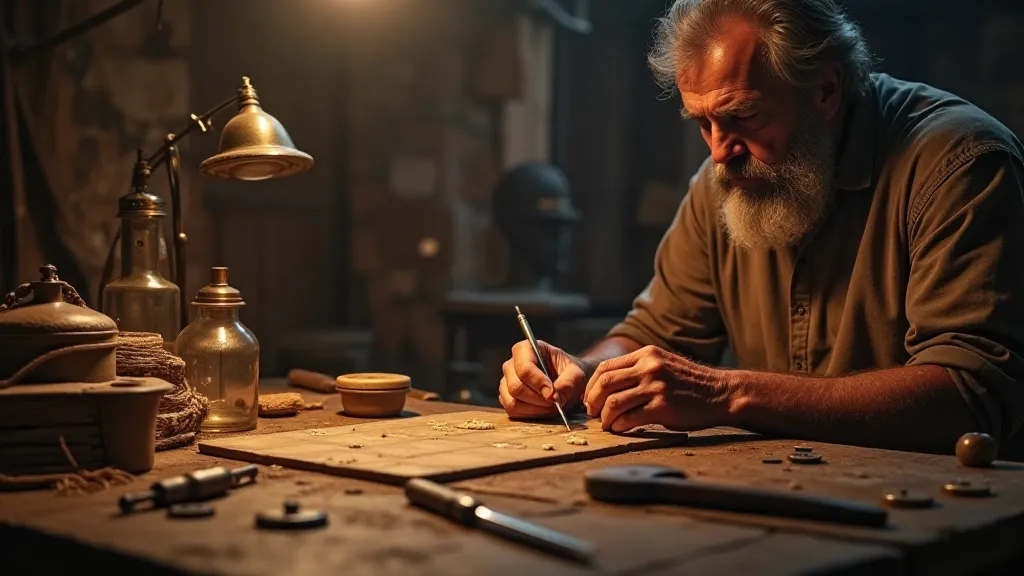
As the Empire expanded, so did the demand for coins. Striking, a process using a blank metal disc hammered between two dies – one bearing the obverse design, the other the reverse – became the dominant method. While simpler and faster than casting, striking still demanded high-quality dies and perfectly prepared blanks. Die-making was a craft in itself, requiring precision engraving and careful selection of metal – often bronze or iron.
The drive for efficiency spurred further innovation. Roman mints began experimenting with different types of molds – reusable molds, molds that could be quickly reproduced, molds that allowed for the production of multiple coins simultaneously. The sophistication of these techniques, often developed incrementally over generations, is truly remarkable.
Recreating History: The Modern Art of Coin Replication
Our modern attempts to recreate Roman coins are, in essence, a continuation of that same quest for precision and efficiency. While industrial casting techniques exist – pressure casting, vacuum casting – many replica creators choose more traditional methods, drawn to the tactile connection with the original techniques. For me, personally, it’s the satisfaction of understanding the historical process, and the challenge of striving for accuracy.
Today, we use a variety of processes, often combining elements of both casting and striking. For example, a detailed master coin is created, often through CNC milling or 3D printing. This master is then used to create a mold – either a two-part mold for casting or a set of dies for striking. The metal – bronze, silver, or even gold – is then melted and poured into the mold or forced between the dies.
The challenge isn't simply about replicating the design; it’s about replicating the *feel* of an ancient coin. The subtle imperfections, the casting flaws, the wear patterns – these all contribute to the authenticity. It’s a delicate balance: striving for accuracy while understanding that perfect replication is an impossible – and perhaps undesirable – goal. The charm of a replica lies in its ability to evoke the spirit of the original, not to be a flawless copy.
My first attempts at creating replicas were... humbling. The metal would warp, the details would be blurred, the surface would be rough. But with each failure, I learned something new – the importance of metal temperature, the need for precise mold alignment, the subtle nuances of metal shrinkage. It’s a process that demands patience, attention to detail, and a willingness to experiment.
Beyond Replication: An Artisanal Renaissance
The fascinating thing about the Roman coin casting industry – and about our modern attempts to recreate it – is the inherent impetus for innovation. The need to produce coins quickly and efficiently led to the development of new techniques, which in turn spurred further refinement. It’s a cycle of constant improvement.
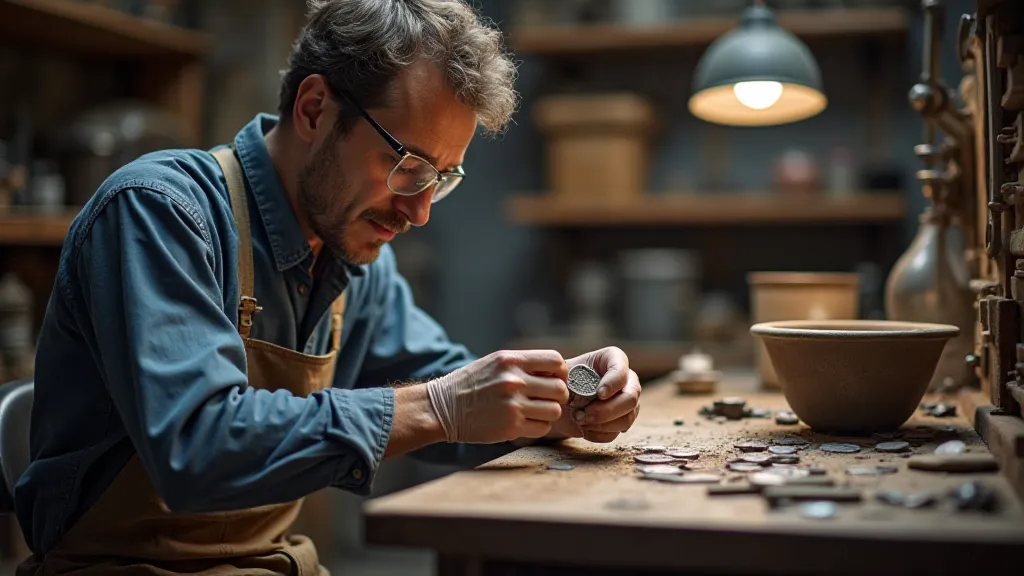
And that same dynamic is at play today. As we grapple with the challenges of digital creation, the resurgence of artisanal craftsmanship offers a compelling counterpoint to mass production. The desire to create something tangible, something imbued with the maker's touch, is a powerful force. Creating Roman coin replicas isn’t just about recreating history; it’s about rekindling that same spirit of ingenuity and artistic dedication that fueled the Roman Empire’s own artisans.
Furthermore, the process of creating these replicas inherently fosters a deeper understanding of ancient history. Examining the iconography, the inscriptions, the metallurgy – it's a holistic learning experience that goes far beyond simply reading about the Roman Empire in a textbook. Collecting these replicas, too, becomes a journey of historical discovery, a tangible connection to a civilization long past.
The Roman coin casting industry, viewed through the lens of modern replica creation, is more than just a footnote in history. It's a testament to the enduring power of human ingenuity, a reminder that even the most seemingly mundane tasks can be transformed into acts of artistic expression. And as we continue to push the boundaries of metal casting techniques, we stand on the shoulders of those ancient artisans, continuing their legacy of innovation and creativity.
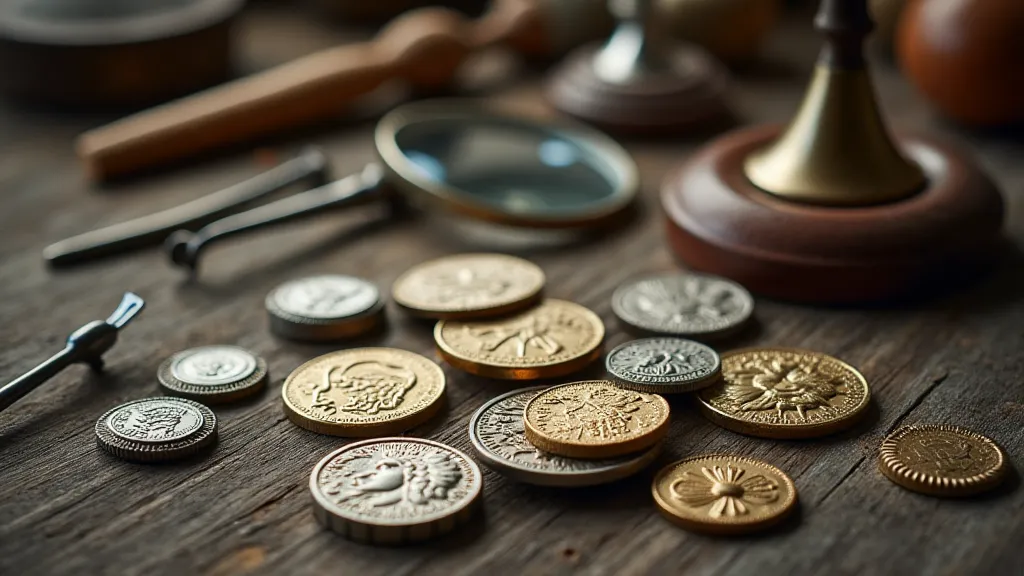